At Borderview Farm in Alburgh, Roger Rainville’s dairy-turned-energy farm makes biodiesel from locally-grown sunflower seeds.
In 2008, when diesel prices rose from $4 to $5 per gallon, Rainville began experimenting with farm-scale biodiesel production. With guidance from UVM Extension and grant funding from the Vermont Bioenergy Initiative, Rainville began planting sunflowers on a portion of his 214 acres and installing biodiesel processing equipment. Oilseed sunflowers (as opposed to confectionary sunflowers that are grown for eating) are the most popular oilseed crop in Vermont, with hundreds of acres planted statewide. The crop is grown in rotation with grains and grasses and yields high quantities of oil.
Harvesting, Cleaning, and Pressing
Following harvest with a combine, a seed cleaner and grain dryer are used to prepare the seeds for storage in a 200-ton grain bin prior to processing. A flex auger system moves the seeds from the storage bin into hoppers on each press, and screw augers push the seed through a narrow dye at the front of the press. Extracted oil oozes from the side of the barrel and is collected in settling tanks while pelletized meal is pushed through the dye at the front and is stored in one-ton agricultural sacks. The oil can then be used as culinary oil for cooking or further refined into biodiesel. The leftover seed meal is used for livestock feed, fuel for pellet stoves, or fertilizer for crops.
Biodiesel Processing
The small-scale biodiesel production facility at Borderview Farm is an 800 square foot insulated and heated building (the space does not need to be heated, but the oil should be stored where it will not freeze) that houses an oil press, a BioPro 190 automated biodiesel processor, a methanol recovery system, and a set of dry-wash columns for cleaning the fuel. The clean oil at the top of each settling tank is added to the BioPro 190 processor along with lye, methanol, and sulfuric acid. The automated processor runs through several stages of processing in about 48 hours (esterification, transesterification, settling, washing, and drying), with one break after 24 hours to remove the glycerin byproduct.
Safety equipment in the processing facility includes personal protective equipment like aprons, gloves, eye protection, a ventilation system, gas detectors, and spill containment materials. At Borderview Farm a set of standard operating procedures hangs on the wall and blank check-sheets are in a binder to make the process easy to repeat. The finished biodiesel is stored in 250 gallon pallet tanks making distribution to different farms easier. The installed capacity of the facility can process 100 tons of seeds from 138 acres of sunflowers per year, yielding 10,500 gallons of biodiesel and 64 tons of sunflower meal (assuming the state average yield of 1,500 pounds sunflower seeds per acre and operation of 24 hours per day for 260 days per year).
Rainville switched from purchasing diesel for five tractors and one truck to making his own biodiesel. He wanted to be independent of imported fuel, and liked creating a new way for farmers to diversify. “Using land for making biodiesel is not the most economical option compared to some other crops, but it’s about creating opportunities to try something different,” says Rainville.
Cost Benefits
Rainville’s annual biodiesel use has ranged from 500 to 3,000 gallons per year. At current prices (over $4 per gallon for diesel and $2.29 per produced gallon of biodiesel) biodiesel has saved him from $500 to $4,000 per year in fuel costs. He also emphasizes energy independence as an added benefit. Plus, any growers that also raise livestock can use the meal, which is leftover after the oil is extracted, as part of their feed rations. Rainville recommends talking with an animal nutritionist to blend this into feed at the right ratio, since sunflower meal has a high fat content.
This story was originally released in a series of energy case studies showcasing farms, businesses, vendors, installers, and technical assistance providers who have made a difference with energy efficiency savings and renewable energy production—all of which are components for helping Vermont reach the renewable energy and environmental impact goals of the Farm to Plate Strategic Plan. Learn more at www.vtfarmtoplate.com.
David Marchant and Jane Sorensen of River Berry Farm—an organic vegetable and fruit producer in Fairfax—were early adopters of biomass heating when they installed a corn and pellet furnace in one of their greenhouses in 2008. The furnace required manual lighting and was snuffed out often when strong winds blew, and did not produce reasonable heat. “I kept thinking, there has got to be a better option,” recalls David, “It was a real labor burden, and you couldn’t count on it.”
Based on their early experiences and bolstered by a commitment to long-term sustainability and reduced fossil fuel dependence, River Berry Farm opted to host a biomass heating demonstration project. This time, they opted for a higher-rated boiler rather than a furnace. Boilers produce hot water, rather than hot air, which allows more options for distributing the heat. The new system also had an automated propane ignition system.
The biomass heating demonstration was part of a UVM Extension project aimed at trialing several furnaces in agricultural heating applications with funding support provided by the High Meadows Fund. According to Chris Callahan, Ag Engineer with UVM Extension Agricultural Engineering Program who assisted with some of the design and performance assessment, “The main lessons learned from these early installations were to buy high quality fuel, seek improved automatic ignition controls, invest in a good chimney and install it well, and know the actual heat output rating of the unit.”
Modern biomass heating appliances generally include a fuel storage bin, an auger for feeding fuel to the appliance, the appliance itself (boiler or furnace) with an ignition system, a combustion chamber, a heat exchanger, and a heat distribution system. They also incorporate some means of controlling combustion, fuel feed rate, and air flow and often include emissions control measures and automated ash removal.
The selected boiler was a Central Boiler Maxim 250 with a 250,000 BTU/hr input rating, efficiency of 87.8%, and EPA Phase II Hydronic Heater qualification. “The boiler makes hot water which we can use in multiple greenhouses by plumbing it to them in insulated PEX piping. Once in the greenhouse, we convert to hot air with a hot water fan coil, put it in the ground for root-zone heating or on the benches in our mat-heating system for starts,” says Marchant. “I like it. I keep trying to find something wrong with it, but I can’t. The payback period is a bit longer due to higher initial costs, but you have to expect that.”
The basic system cost was approximately $13,000 for the boiler, bin, pad, and plumbing to a hot water fan coil. The other heat distribution systems included in-ground PEX, heat exchange, and plumbing for a bench heat system and added approximately another $5,000. The system is more automated and reliable than the earlier furnace was, but the higher initial costs and the fact that the system is only used 3 months out of the year do prolong the payback period to about 12 years when compared with a propane furnace. If the system was used for 6 (space heating) or even 12 months (wash water, pasteurization) of the year the payback would be halved or quartered, respectively.
“In addition to the financial payback, the carbon emissions avoidance is also of interest to many people,” says Callahan, “In River Berry Farm’s case, the Maxim is helping them avoid 5,910 pounds of net CO2 emissions per year which is about equivalent to 5,000 miles car travel or the CO2 sequestered by half an acre of pine forest.”
Learn more about UVM Extension’s Agricultural Engineering Program at.
This story was originally released in a series of energy case studies showcasing farms, businesses, vendors, installers, and technical assistance providers who have made a difference with energy efficiency savings and renewable energy production—all of which are components for helping Vermont reach the renewable energy and environmental impact goals of the Farm to Plate Strategic Plan. Learn more at www.vtfarmtoplate.com.
Efficiency Vermont, Renewable Energy Resource Center, Renewable Energy Vermont and Clean Energy Development Fund combine efforts to bring up to $5,500 in rebates to Vermonters who heat local
Through a generous opportunity, Vermonters now have a short-time frame before the new year to capitalize on a fantastic incentive offering that helps them save money, while supporting Vermont jobs and sustainable forests, while making sure they stay warm this winter.
Vermonters can get up to $5,500 to help switch from fossil fuel to local wood heating. Cash incentives are available from the Clean Energy Development Fund and Efficiency Vermont. Renewable Energy Vermont and the Renewable Energy Resource Center have partnered to help promote the incentives.
“We’ve been very happy with our decision to switch to a wood pellet boiler. Not only do we save money every year on our fuel bill, but we also love the fact that we’re helping to keep forests intact and logging jobs going,” says Mark Bushnell of Middlesex.
Vermonters who make the switch to wood pellet fuel typically save $1,500 annually when compared to oil and propane fuel heating options. And for those who are used to whole-home heating through their traditional boiler, the wood pellet boiler keeps it simple and complete. Advanced wood pellet boilers are fully automatic, so there’s no work for the home or business owner.
“I heated my home for years with a standard wood stove, but I’m happier with my wood pellet boiler. The new boiler is much more efficient and better for the environment because it is cleaner burning. And it feels great to be off fossil fuels,” says Susan Clark of Middlesex.
Wood pellet boilers, though not well known in the United States, are the primary way of heating in some parts of the world, including Upper Austria where more than 40,000 homes and businesses heat with wood from their background in an easy, seamless way. In fact, the State of Vermont and Upper Austria are involved in a Sister Statehood Agreement to help learning across both sides of the Atlantic to increase the uptake of this sustainable, local heating option.
“For many years, Vermont has been a national leader in the use of modern wood heating systems in large buildings like schools, office buildings, and apartment buildings. With pellets now available in bulk using specialized delivery trucks that conveniently blow pellets into a fuel bin and heating systems that are fully-automated, many homeowners and small businesses are also making the switch from oil and propane,” said Adam Sherman of the Biomass Energy Resource Center.
For more information, please go to www.advancedwoodheat.com
Media Contacts:
Renewable Energy Vermont, Ansley Bloomer, ansley@revermont.org (802) 595-0723
Biomass Energy Resource Center, Alayna Howard, ahoward@veic.org (802) 540-7656
Renewable Energy Resource Center, Alayna Howard, ahoward@veic.org (802) 540-7656
Efficiency Vermont, Alayna Howard, ahoward@veic.org (802) 540-7656
Clean Energy Development Fund, Andrew Perchlik, andrew.perchlik@state.vt.us (802) 828-4017
In early 2014 Full Sun Company, a small start-up business was co-founded by Netaka White and Davis McManus. Fueled by an interest to help family farms grow, Full Sun began processing sunflower and non-GMO canola oil crops into specialty food-grade oil and high-protein meal for the farmers. Sunflower and canola oil distribution picked up quickly through local CSAs, farm stores, specialty food shops, health and wellness centers, and direct sales to chefs in the Northeast.
Netaka White previously served as the Vermont Bioenergy Initiative’s (VBI) program director, which directly helped to develop the business model to nurture farm partnerships, both as growers and recipients of oilseed meal – the other product that’s generated from making the oil. At Full Sun oilseeds are pressed with large mechanical machinery, producing oil and a granular meal. The team at Full Sun Company learned a lot about seed storage and oil pressing from the early VBI grantees, such as John Williamson of State Line Farm, and Roger Rainville of Borderview Farm.
The first of the two products, the seed meal, has been used as fuel for pellet stoves, or as is the case with Full Sun, sold as fertilizer for crops, or nutritional meal for livestock. At full operation, Full Sun can pump out one ton of meal per day – necessary to meet the growing demand of such customers as The Intervale in Burlington, Vermont and several local pig, poultry, dairy, and beef producers.
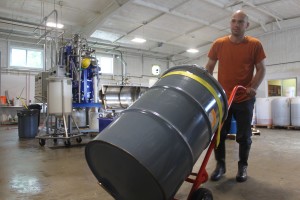
Full Sun Company employee, Zach Hartlyn, moves an off-spec oil barrel for biodiesel production
Credit: Full Sun Company
The second product, the oil, is used as culinary oil for cooking. Staying true to their commitment to an extraordinary culinary product, Full Sun Company diverts any of the oil that does not meet their standards to Vermont Bioenergy Initiative biofuel producers to undergo further processing and become biofuel. Approximately 250-300 gallons of off-spec oil for biodiesel has been processed since February, 2014.
In October, 2014, Full Sun Company halted operation to make room for growth to meet the increased demand for their products and scale up to align with Vermont’s accelerating agricultural economy. White and McManus acquired the former Vermont Soap building in Middlebury, Vermont in order to build a full scale mill and achieve their anticipated greater capacity. Over the course of one of the coldest winters in recent history, the Full Sun team made the renovations and adjustments needed to repurpose the building into the first non-GMO verified oil mill in New England. By March of 2015 Full Sun Company had pressed sunflower and canola seeds to make their first batch of specialty oils. The new operation can yield 130 gallons of oil per day – about 2600 gallons per month!
With no shortage of innovation or ambition, White notes, “David and I are in this with the interest of having a transformative effect on local agriculture and food systems.” Well on their way, the operation is certified GMO free, and the next steps are being taken towards becoming certified organic.
As they grow, Full Sun would like to buy from local grower-suppliers and work with local businesses to package and label feed to be distributed to farmers of varying sizes, from backyard chicken growers to larger operations. Collaborating with Vermont breweries and distilleries is also in queue. Full Sun is working with one local distillery to put together “a package” for farmers so they have markets for profitable grain crops throughout four years of rotation (rye, wheat, sunflowers, etc.) and can offer farmers the indexed prices for these locally grown grains and oilseeds.
27 Jul 2015
Summit on Creating Prosperity and Opportunity Confronting Climate Change – Looking Back and Looking Forward
The Summit on Creating Prosperity and Opportunity Confronting Climate Change brought together over 400 innovative business, non‐profit, and community leaders, elected officials, public policy advocates, students, and interested residents to begin to frame policy and investment strategies to advance the development of the Vermont Climate Economy. Summit participants developed a list of key practical actions to serve as a launching point for the Vermont Climate Change Economy Council (VCCEC), a group charged with a one year mission to develop a structured plan with practical actions to reduce carbon emissions and stimulate green economic development in Vermont. The Council will build a set of public/private strategies designed to promote economic opportunity, innovative business development, investment, and job creation in Vermont.
Over the course of 2015, VCCEC will evaluate findings, key ideas and suggested action steps derived from the Summit, lead regional public forums, evaluate and summarize research findings, interview key stakeholder groups, and consider model economic development strategies from other state and countries. During 2015, the group will develop a strategic platform of recommendations for action, and report to the Vermont legislature, the Governor of Vermont and the public in January 2016. The Vermont Council on Rural Development (VCRD) will provide support to their work and then help promote the platform of action that comes from its deliberants. Goals of the Vermont Climate Change Economy Council are to:
- Identify opportunities created by climate change to strengthen Vermont’s economy through strategies advancing key business clusters and economic sectors.
- Build an increased sense of unity in Vermont around policies to confront and mitigate the impact of climate change and to advance economic opportunities and solutions that respond to climate change.
- Build a public information campaign to celebrate innovation and Vermont’s green business leadership; internally and externally marketing to build the Vermont brand as an economic/environmental problem solver.
- Expand Vermont’s economic brand around climate change solutions to retain and attract youth and creative entrepreneurs to locate throughout the state.
Vermont businesses and nonprofits are addressing climate change – both its challenges and opportunities. Their creative solutions are a growing part of our state’s economy. What are your experiences? Do you have ideas about how Vermont can grow jobs and nurture innovative business development in sectors ranging from clean energy, to recycling, transportation systems, and thermal efficiency?
Join the Vermont Council on Rural Development and local business leaders at a forum on “What’s Next for Vermont’s Climate Change Economy?” Forums will take place at 7:00pm at the Paramount in Rutland (Aug 26), the Latchis Hotel in Brattleboro (Oct 6), and City Hall in Burlington (Oct 29). Come to the forum(s) most convenient for you.
These forums are the next step for public input to the Vermont Climate Change Economy Council, a group working to develop a practical plan to reduce carbon emissions and stimulate economic development in Vermont. To learn more about the forums and the Council visit VCRD’s website at vtrural.org, download the event flyer (pdf).
For more information about the results of the summit, Click HERE to read the report and follow the hashtag #VTClimateEconomy and Vermont Council on Rural Development on Twitter at @VTRuralDev for more updates!
Farms open their doors to a public interested in learning more about where food comes from and supporting the local agricultural economy
Farmers across Vermont will throw open their barn doors and garden gates to welcome the public for a behind-the-scenes look at Vermont’s vibrant working landscape. Vermont’s first Open Farm Week will be held Monday, August 3 – Sunday, August 9, 2015.
Open Farm Week is a weeklong celebration of Vermont farms. Over 100 farms are participating, many of whom are not usually open to the public. Open Farm Week offers Vermonters and visitors alike educational opportunities to learn more about local food origins, authentic agritourism experiences, and the chance to build relationships with local farmers. Activities vary and may include milking cows and goats, harvesting vegetables, collecting eggs, tasting farm fresh food, scavenger hunts, hayrides, farm dinners, and live music.
Visit DigInVT for a map of participating farms by region. Many events are free and costs vary depending on what activities are offered. Everyone is invited to join the #VTOpenFarm conversations on social media. All participating farms, geographic location, and offerings are at www.DigInVT.com.
Farmers’ markets will also be a part of the Open Farm Week celebration as organizers planned the event to coincide with National Farmers’ Market Week – also the first week of August.
The first Vermont Buy Local Market on the Statehouse Lawn will be held during Open Farm Week on Tuesday, August 4th from 10am-1pm. The Vermont Agency of Agriculture, Food and Markets is organizing the first Statehouse farmers’ market in collaboration with the Capital City Farmers’ Market and NOFA-VT.
Building off of the success of NOFA-VT’s 2014 Open CSA Farm Day, Open Farm Week is a collaborative statewide agritourism project organized by members of the Vermont Farm to Plate Network including Intervale Center, Vermont Farm Tours, Neighboring Food Co-op Association, Vermont Agency of Agriculture, Vermont Fresh Network, Vermont Department of Tourism, Shelburne Farms and Farm-based Education, NOFA-VT, and City Market. Open Farm Week helps Vermont reach its statewide Farm to Plate food system plan goals to increase farm profitability, local food availability, and consumption of Vermont food products.
Vermont Open Farm Week is made possible by the generous support of Premiere Sponsor: City Market/Onion River Coop as well as the Vermont Department of Tourism and Marketing; Vermont Agency of Agriculture, Food and Markets, Localvore Today and Woodchuck Hard Cider.
29 Jun 2015
Soybeans for On-farm Biodiesel Production
Mark Mordasky, owner of Rainbow Valley Farm in Orwell, Vermont has been growing soybeans as a cash crop and for on-farm biodiesel and animal feed since 2008. When fuel prices began to climb, Mark took initiative and started searching for an innovative and more cost efficient way to meet his farm’s energy demands. The Vermont Sustainable Jobs Fund was able to help Mark take his first steps towards sustainable biofuel production. Mark is able to press these soybeans after harvesting and make two distinct products, oil and meal. The meal is an instantly marketable product and can be sold as feedstock or organic fertilizer; the oil will be further processed into biodiesel.
Soybeans crops are well suited for biodiesel production in Vermont and perform best in heavy soil like those found in Addison County, as University of Vermont Extension Agronomist, Heather Darby explains. Soybeans don’t always do well in in light, well drained soils, and as with any crop the best way to understand the demands of any crops is to contact your University Extension and have your soil tested. Additionally, because soybeans are a legume, they produce nitrogen in association with bacteria, meaning that these crops don’t require the application of additional nitrogen to produce a high yield. These low input, high yield crops are fairly easy to grow, are well suited to the Vermont climate, and afford farmers flexible planting dates. Heather and the rest of the UVM Extension team have seen yields ranging from 35 bushels per acre to up to 85 bushels per acre with varying practices.
In the below video, Mike Mordasky shares his experience and knowledge of soybean production from planting through harvesting harvest and beyond to storage and the creation of the final products. In addition, Heather Darby shares here insights into maturity groupings, variety selection, and best growing practices.
08 Jun 2015
Grass Energy in Vermont
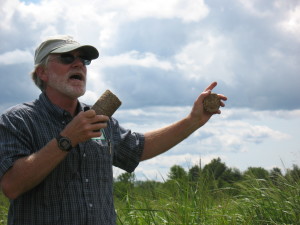
University of Vermont Extension Agronomist, Sid Bosworth explains in the field his research into use of grasses for combustion and thermal energy
In 2008, the Vermont Bioenergy Initiative began to explore the potential for grasses energy grown in Vermont to meet a portion of the state’s heating demand and reduce the consumption of non-renewable fossil fuels. The Grass Energy in Vermont and the Northeast report was initiated by the Vermont Sustainable Jobs Fund, and carried out by its program the Vermont Bioenergy Initiative, to aid in strategic planning for future grass energy program directives.
Grass Energy in Vermont and the Northeast summarizes current research on the agronomy and usage potential of grass as a biofuel, and points to next steps for the region to fully commercialize this opportunity. The keys to commercializing grass for energy are improving fuel supply with high-yielding crops, establishing best practices for production and use, developing appropriate, high-efficiency combustion technology, and building markets for grass fuel.
Perennial grasses, while serving as a biomass feedstock for heating fuel, also have numerous other benefits to farmers. The grass energy benefits reviewed in the report include retaining energy dollars in the local community, reducing greenhouse gas emissions from heating systems, improving energy security, providing a use for marginal farmland, and reducing pollution in soil and run-off from farms.
Regional and closed loop processing were two models recommended by the report, both involving farmers growing and harvesting grass, but differing in where the grass is processed into fuel and where it is used. The regional processing model calls for aggregating grass from a 50-mile radius at a central processing facility, where the grass is made into and used as fuel, or sold to local users. The closed loop model suggests farmers growing and processing grass on-site for on-farm or community use. Other models, like mobile on-farm processing and processing fuel for the consumer pellet market have significant hurdles to overcome if they are to be successful in Vermont.
In the below video a Vermont agronomist explains switchgrass production followed by entrepreneurs turning bales of grass into briquette fuel. This grass biofuel feedstock can be grown alongside food production on marginal agricultural lands and abandoned pastures, and in conserved open spaces. The harvested grass can be baled and used as-is in straw bale combustion systems, or it can be compressed into several useable forms for pellet fuel combustion systems.
For more information on grass biofuel feedstocks and to read the full Grass Energy in Vermont and the Northeast report visit the grass energy section of the Vermont Bioenergy website.
01 Jun 2015
Food Versus Fuel – Local Production for Local Use – Biodiesel as Part of Sustainable Agriculture
Nationally, corn-based ethanol and palm oil based biodiesel are gaining negative attention for their impacts on the environment and food security. But here in Vermont, farms are producing on-farm biodiesel to power equipment and operations on the farm and the local farm community. This is a profoundly different model from national and international biofuel production. Agricultural Engineering and Agronomy Researchers at University of Vermont Extension in partnership with farmers and the Vermont Bioenergy Initiative have developed a model of local minded, on-farm production of biofuels that can help rural communities transition away from unsustainable models of food, feed and fuel production.
National and global models of corn-ethanol and soy oil-biodiesel production are resulting in large-scale land conversions in some parts of the world, in particular to a loss of native grass and forestland. This type of biofuel production is not happening in Vermont, where bioenergy production incorporates rotational oilseed crops like sunflowers and soybeans on Vermont farms.
Locally produced biodiesel supports resiliency in Vermont, a cold climate state which is particularly dependent on oil. Over $1 billion leaves the state for heating and transportation fuel costs. Heating and fuel independence by producing on-farm biodiesel provides farmers fuel security which is comparable to that which is sought by Vermont’s local food movement.
The local production for local use model results in two products from one crop: oil and meal (animal feed or fertilizer). By growing oilseed and pressing the seed to extract the oil, farms are creating a valuable livestock feed at home, rather than importing it. The oil can be sold as a food product, used directly in a converted engine or converted to biodiesel for use in a standard diesel engine. In this way, oilseed crops offer flexibility in the end-use of the products. US corn-based ethanol mandates are raising grain costs nationally, making feed expensive for Vermont farmers. Local bioenergy production means farmers produce their own feed, fuel, and fertilizer for on-farm use, at a fraction of the cost and more stable prices. Reduced and stable prices for feed, fuel, and fertilizer can mean improved economic viability for Vermont farms and more stable food prices for Vermont consumers in the future.
Overall viability can be seen in the local production for local use model by considering economics, energy and carbon emissions. Biodiesel production costs of between $0.60 and $2.52 per gallon have been estimated for farm-scale production models, which are generally below market price for diesel fuel. The net energy return in Vermont on-farm biodiesel operations has been estimated at between 2.6 and 5.9 times the invested energy (i.e. more energy out than was required to produce the fuel), demonstrating strong returns and potential for improvement with increased scale. Furthermore, oilseed-based production of biodiesel has been estimated to result in a net reduction of carbon dioxide emissions of up to 1420 lbs. per acre, the equivalent of about 1500 miles of car travel per year.
Categorizing the Vermont biofuel model with national models and trends is inaccurate, considering the innovative and efficient systems benefiting Vermont farmers. While national and international analysis weighs the benefits of food versus fuel, the model is quite unique in Vermont and the food versus fuel challenge is well met. The model developed in Vermont does however have wider-reaching implications in that this can be replicated in rural farm communities across the US.
As John Williamson of Stateline Farm, a Vermont Bioenergy grant recipient says, “100 years ago everyone produced their own fuel; we are just doing that now in a different way.”
19 May 2015
Mitigating Potential Biomass Feedstock Pests
The Vermont Bioenergy Initiative aims to connect diversified agriculture and local renewable energy production for on-farm and community use by supporting research, technical assistance, and infrastructure development in emerging areas of bioenergy including biodiesel production and distribution. As we move into the growing season, there are a variety of pests that can potentially affect sunflower, canola, and soybean biomass feedstock production. In this video a University of Vermont agronomist explains how to control theses potential biomass feedstock pests and increase crop, and eventually biofuel, yields without heavy reliance on pesticides and herbicides.