Following the Fall Semester UVM bioenergy course Bioenergy: Biomass to Biofuels, the University of Vermont will be offering a new bioenergy course this spring entitled Waste to Energy: Community Development Application. The course will again be taught by Anju Dahiya, cofounder of General Systems Research, LLC (GSR), lead biofuels instructor at the University of Vermont’s Rubenstein School of Environment and Natural Resources, and a Vermont Bioenergy Initiative algae for biofuel grant recipient. This course is open to both degree and non-degree students from any background or department, as well as farmers, entrepreneurs, and teachers interested in developing curriculum, or projects at school or college levels. This course is also approved for graduate credit.
In a Vermont post Act 148, the universal recycling law for solid waste, food waste, dairy farm manure, municipal wastes, landfill waste, carbon exhaust, nutrient runoff and other materials not being converted into value products are all resources that hold potential energy that can be developed in a sustainable way to power a local economy. This class focusing on waste sourced bioenergy comes on the heels of a promising results and continued work by Dahiya’s company GSR on incorporating algae into Green Mountain Power’s anaerobic digester at Nordic Farms in Shelburne, Vermont. The product serves as a strong example in which excess nitrogen and phosphorus in cow manure would find its way off farmland and end affecting health of natural water bodies, but instead is harnessed to make electricity and biofuel. As listed in the course catalog “the mission of this program is to provide hands-on instruction in all possible Bioenergy areas, support generation of related skilled workforce and stimulate sustainable energy production.”
Lectures will be held every on campus every Friday during the UVM spring semester from 12:00 pm to 3:00 pm, with 5 additionally required off campus field trips. The course required textbook, Bioenergy: Biomass to Biofuels, was edited by Anju Dahiya less than a year ago and represents a compilation of work from an extensive list of well-respected university extension programs, such as The University of Vermont Research Extension, as well as numerous national organizations including the US Department of Energy’s National Renewable Energy Laboratories.
Learn more about this course at the University of Vermont Renewable BioEnergy page or email the lead instructor Anju Dahiya at adahiya@uvm.edu.
19 Oct 2015
Field to Flue Open House at Meach Cove Farms
Vermont-grown grasses are being used to heat the Biomass Building – a 4,200 square foot commercial building at Meach Cove Farms in Shelburne. Local residents, community leaders, and renewable energy enthusiasts are invited to visit Meach Cove Farms Friday, October 23 – Saturday, October 24 for an Open House to learn how grass pellets are generating heat in a biomass boiler – an emerging source of bioenergy in Vermont.
Meach Cove Farms is a 1,000-acre certified organic farm primarily growing soy beans, wheat, rye, and corn as well as wine grapes, woodlands, and switchgrass trial plots for use in grass energy production. The Open House will offer a complete demonstration of the Grass Pellet Heating Equipment Combustion Optimization project – the first project in New England to showcase grass test plots, densification equipment, and an EvoWorld biomass boiler that burns the grass.
Meach Cove Farms began collaborating with Dr. Sidney Bosworth of the University of Vermont College of Agriculture and Life Sciences and the Vermont Bioenergy Initiative in 2009 to assess the potential of different species of grass as solid biofuel for heating applications.
In September 2011 Meach Cove Farms was awarded an USDA Natural Resources Conservation Service Conservation Innovation Grant to research the feasibility of Vermont grown grass pellets and heating equipment potential as an emerging renewable energy source in Vermont. The biomass boiler being featured at the Open House was funded through a Conservation Innovation Grant (CIG) administered by the Natural Resources Conservation Services.
IF YOU GO:
Meach Cove Farms is located at 310 Beach Road in Shelburne (off Bostwick Road, 1.6 miles west of Rte 7). The Open House runs from 9 am – 12 noon both Friday and Saturday, October 23-24. There is no cost and both days are open to the public. More info at www.meachcovefarms.org, 802-985-9218.
David Marchant and Jane Sorensen of River Berry Farm—an organic vegetable and fruit producer in Fairfax—were early adopters of biomass heating when they installed a corn and pellet furnace in one of their greenhouses in 2008. The furnace required manual lighting and was snuffed out often when strong winds blew, and did not produce reasonable heat. “I kept thinking, there has got to be a better option,” recalls David, “It was a real labor burden, and you couldn’t count on it.”
Based on their early experiences and bolstered by a commitment to long-term sustainability and reduced fossil fuel dependence, River Berry Farm opted to host a biomass heating demonstration project. This time, they opted for a higher-rated boiler rather than a furnace. Boilers produce hot water, rather than hot air, which allows more options for distributing the heat. The new system also had an automated propane ignition system.
The biomass heating demonstration was part of a UVM Extension project aimed at trialing several furnaces in agricultural heating applications with funding support provided by the High Meadows Fund. According to Chris Callahan, Ag Engineer with UVM Extension Agricultural Engineering Program who assisted with some of the design and performance assessment, “The main lessons learned from these early installations were to buy high quality fuel, seek improved automatic ignition controls, invest in a good chimney and install it well, and know the actual heat output rating of the unit.”
Modern biomass heating appliances generally include a fuel storage bin, an auger for feeding fuel to the appliance, the appliance itself (boiler or furnace) with an ignition system, a combustion chamber, a heat exchanger, and a heat distribution system. They also incorporate some means of controlling combustion, fuel feed rate, and air flow and often include emissions control measures and automated ash removal.
The selected boiler was a Central Boiler Maxim 250 with a 250,000 BTU/hr input rating, efficiency of 87.8%, and EPA Phase II Hydronic Heater qualification. “The boiler makes hot water which we can use in multiple greenhouses by plumbing it to them in insulated PEX piping. Once in the greenhouse, we convert to hot air with a hot water fan coil, put it in the ground for root-zone heating or on the benches in our mat-heating system for starts,” says Marchant. “I like it. I keep trying to find something wrong with it, but I can’t. The payback period is a bit longer due to higher initial costs, but you have to expect that.”
The basic system cost was approximately $13,000 for the boiler, bin, pad, and plumbing to a hot water fan coil. The other heat distribution systems included in-ground PEX, heat exchange, and plumbing for a bench heat system and added approximately another $5,000. The system is more automated and reliable than the earlier furnace was, but the higher initial costs and the fact that the system is only used 3 months out of the year do prolong the payback period to about 12 years when compared with a propane furnace. If the system was used for 6 (space heating) or even 12 months (wash water, pasteurization) of the year the payback would be halved or quartered, respectively.
“In addition to the financial payback, the carbon emissions avoidance is also of interest to many people,” says Callahan, “In River Berry Farm’s case, the Maxim is helping them avoid 5,910 pounds of net CO2 emissions per year which is about equivalent to 5,000 miles car travel or the CO2 sequestered by half an acre of pine forest.”
Learn more about UVM Extension’s Agricultural Engineering Program at.
This story was originally released in a series of energy case studies showcasing farms, businesses, vendors, installers, and technical assistance providers who have made a difference with energy efficiency savings and renewable energy production—all of which are components for helping Vermont reach the renewable energy and environmental impact goals of the Farm to Plate Strategic Plan. Learn more at www.vtfarmtoplate.com.
Efficiency Vermont, Renewable Energy Resource Center, Renewable Energy Vermont and Clean Energy Development Fund combine efforts to bring up to $5,500 in rebates to Vermonters who heat local
Through a generous opportunity, Vermonters now have a short-time frame before the new year to capitalize on a fantastic incentive offering that helps them save money, while supporting Vermont jobs and sustainable forests, while making sure they stay warm this winter.
Vermonters can get up to $5,500 to help switch from fossil fuel to local wood heating. Cash incentives are available from the Clean Energy Development Fund and Efficiency Vermont. Renewable Energy Vermont and the Renewable Energy Resource Center have partnered to help promote the incentives.
“We’ve been very happy with our decision to switch to a wood pellet boiler. Not only do we save money every year on our fuel bill, but we also love the fact that we’re helping to keep forests intact and logging jobs going,” says Mark Bushnell of Middlesex.
Vermonters who make the switch to wood pellet fuel typically save $1,500 annually when compared to oil and propane fuel heating options. And for those who are used to whole-home heating through their traditional boiler, the wood pellet boiler keeps it simple and complete. Advanced wood pellet boilers are fully automatic, so there’s no work for the home or business owner.
“I heated my home for years with a standard wood stove, but I’m happier with my wood pellet boiler. The new boiler is much more efficient and better for the environment because it is cleaner burning. And it feels great to be off fossil fuels,” says Susan Clark of Middlesex.
Wood pellet boilers, though not well known in the United States, are the primary way of heating in some parts of the world, including Upper Austria where more than 40,000 homes and businesses heat with wood from their background in an easy, seamless way. In fact, the State of Vermont and Upper Austria are involved in a Sister Statehood Agreement to help learning across both sides of the Atlantic to increase the uptake of this sustainable, local heating option.
“For many years, Vermont has been a national leader in the use of modern wood heating systems in large buildings like schools, office buildings, and apartment buildings. With pellets now available in bulk using specialized delivery trucks that conveniently blow pellets into a fuel bin and heating systems that are fully-automated, many homeowners and small businesses are also making the switch from oil and propane,” said Adam Sherman of the Biomass Energy Resource Center.
For more information, please go to www.advancedwoodheat.com
Media Contacts:
Renewable Energy Vermont, Ansley Bloomer, ansley@revermont.org (802) 595-0723
Biomass Energy Resource Center, Alayna Howard, ahoward@veic.org (802) 540-7656
Renewable Energy Resource Center, Alayna Howard, ahoward@veic.org (802) 540-7656
Efficiency Vermont, Alayna Howard, ahoward@veic.org (802) 540-7656
Clean Energy Development Fund, Andrew Perchlik, andrew.perchlik@state.vt.us (802) 828-4017
The Vermont Bioenergy Initiative connects diversified agriculture and local renewable energy production for on-farm and community use by supporting research, technical assistance, and infrastructure development in emerging areas of bioenergy including biodiesel production and distribution for heating and transportation, oil crops for on-farm biodiesel and feed, grass for heating, and algae production for biofuels and wastewater management. Explore the initiative’s extensive and accessible set of bioenergy resources for replication in rural communities across the United States and beyond.
Video
A series of informative educational showcase a range of biofuel possibilities; from research and crop farming to feedstocks and fuel. The videos were developed by the Vermont Sustainable Jobs Fund, UVM Extension researchers, KSE Partners, and the Vermont Bioenergy Initiative grantees.
Calculators
Two calculators, developed by UVM Extension, help connect potential costs and profits associated with oilseed production:
- Grass Biomass Production and Harvest Cost Estimator
- Vermont Oilseed Crop Production Cost and Profit Calculator
Course Work
- Biomass to Biofuels, University of Vermont: This semester-long course covers liquid and solid biofuels, biogas and bio-electricity, and environmental, social and economic issue related to biofuels. The course includes guest lecturers and field days. Available for variable credits.
- Biomass to Biofuels, Vermont Technical College: The development of this course and associated materials led to an online repository of resources for the classroom covering biomass to biofuels.
- Digester Operations Master Certificate, Vermont Technical College: a twelve week program designed for participants to work directly with operations staff of Vermont Tech’s anaerobic digester and come away with understanding of the mechanics and operations of a digester system, as well as other areas such as permitting, regulatory compliance and record keeping.
- Alternative Fuel Vehicles: Biodiesel, part of the Green Trainings series at Vermont Technical College: This 2-day course covers engine systems, biodiesel blends and biodiesel production, including a demonstration of fuel-making equipment.
- Biofuels Course at Yestermorrow Design/Build School, part of the Green Trainings series at Vermont Technical College: This weekend workshop enables students to begin replacing fossil fuels with biofuels, such as adapting engines to run on straight vegetable oil. 1 credit.
Textbook
Bioenergy: Biomass to Biofuels; is an innovative new textbook that provides insight into the potential and current advances and benefits of biofuel. Contributions include an extensive list of well-respected university extension programs, such as The University of Vermont Research Extension, as well as numerous national organizations including the US Department of Energy’s National Renewable Energy Laboratories.
Reports
A variety of reports are available which cover a range of topics including seed preparation and storage:
- Institute for Energy and the Environment at Vermont Law School.Legal & Regulatory Review of On-farm Biodiesel Production. 2015.
- Chris Callahan and Netaka White,Vermont On-Farm Oilseed Enterprises: Production Capacity and Break-even Economics. July 2013.
- Nell Campbell, Local Production for Local Use to Supply a Portion of Vermont’s Energy Needs.May 2009.
- Emily J. Stebbins. Technical and Economic Feasibility of Biodiesel Production in Vermont: Evidence From a Farm-Scale Study and a Commercial-Scale Simulation Analysis. May 2009.
- Christopher W. Callahan,A Feasibility Analysis of a Mobile Unit for Processing Oilseed Crops and Producing Biodiesel in Vermont. December 2008.
- Emily Stebbins, The Market Potential of Farm-Scale Oilseed Crop Products in Vermont. February 2008. (See also the Executive Summary)
- John Williamson & Tanner Williamson – State Line Biofuels, LLP, Chris Callahan – Callahan Engineering, PLLC, Feasibility Analysis:_Solar Seed Dryer and Storage Bin at State Line Farm, Bennington, VT. October 2008
- Christopher W. Callahan, A Feasibility Study of a Mobile Unit for Processing Oilseed Crops and Producing Biodiesel in Vermont. December 2008
- Kenneth Mulder, Ph.D., Galen Wilkerson, Emily J. Stebbins.Homegrown Fuel: Economic Feasibility of Commercial-Scale Biodiesel Production in Vermont. September 2007.
- The Vermont Biodiesel Project: Building Demand in the Biofuels Sector – Final Report. October 2006. (See also theExecutive Summary)
- Vermont Department of Buildings and General Services, Vermont Biodiesel Pilot Project: Emissions Testing of Biodiesel Blends With #6 Fuel Oil At the Waterbury State Office Complex – Final Report. September 2006.
- Laboratory and Field Testing of Biodiesel in Residential Space Heating Equipment – Final Report. August 2006.
- Vermont Biodiesel Supply Chain Survey – Final Report. April 2006.
- Wilson Engineering,Grass Energy in Vermont and the Northeast, May 2014.
Technical Advice
Connect directly with the Vermont Bioenergy Initiative’s technical assistance providers:
Oilseeds for Biofuel
- Heather Darby, Agronomic and Soils Specialist
- University of Vermont Extension, Northwest Crops and Soils Team
- (802) 524-6501
- darby@uvm.edu
- Chris Callahan, PE, Agricultural Engineer
- University of Vermont Extension
- (802) 773-3349
- callahan@uvm.edu
Grass for Heating Fuel
- Sidney Bosworth, Extension Professor
- University of Vermont College of Agriculture and Life Sciences
- (802) 656-0478
- bosworth@uvm.edu
Algae for Biodiesel
- Anju Dahiya, Instructor and Principal
- University of Vermont and GSR Solutions
- (802) 310-1936
- adahiya@uvm.edu
17 Aug 2015
The Third Annual National Bioenergy Day
The Third Annual National Bioenergy Day (NBD), which will take place Wednesday, October 21st, is a day that is marked with events from across the country that celebrates energy independence, local jobs, and many other benefits of local bioenergy. Led by Biomass Power Association in partnership with U.S. Forest Service, National Bioenergy Day is an opportunity for Vermonters to showcase our research, progress, and impacts in producing local bioenergy for local use.
How To Get Involved:
- Organize an event on or near October 21ndthat showcases bioenergy as a clean, efficient, and resourceful way to produce energy. Emphasizes bioenergy’s role in improving environmental health; and facilitates collaboration along the supply chain.
- Partner with someone who works in the bioenergy supply chain to create an event. Use the Vermont Energy Atlas to find partners in your area.
- Piggyback on an existing event and call it a NBD event.
- Share and talk about NBD in your social media and press efforts while promoting impacts in your community.
The Vermont Bioenergy Initiative, for example, will spend the day re-capping and previewing events and research on our Twitter handle @VTBioenergy that took place throughout the summer and that are planned for the fall. We’ll be recapping and sharing exciting things like the exciting learning opportunities at the University of Vermont, Full Sun Company’s Biodiesel and Meal production, and much more!
For more information, you can visit also visit bioenergyday.com and follow @USAbiomass on twitter!
Click Here for National Bioenergy Day Participation Guide!
10 Aug 2015
Bioenergy Events 2015
The team at Vermont Bioenergy Initiative has worked to put together a comprehensive list of bioenergy events for you! This list will be updated as more events arise. If you know a bioenergy events that you think should be on the list, tweet it to us! @VTbioenergy
- September
- Modern Wood Pellet Heating Forum, Tuesday, Sep. 15, 2015, 6 – 8:30pm, Montshire Museum in Norwich, Vermont
- Ag Innovation Showcase September 14-16, 2015 St. Louis, MO
- 2nd International Conference on Past and Present Research Systems of Green Chemistry. September 14-16, 2015. Orlando, Florida
- Switchgrass III. September 30 to October 2, 2015. Knoxville, TN
- Algae Biomass Summit September 30-October 2, 2015 Washington, DC
- October
- Renewable Energy 2015 Conference & Expo. October 8-9 2015. Burlington, VT
- National Advanced Biofuels Conference & Expo. October 26 – 28, 2015. Omaha, Nebraska
- 2015 TAPPI PEERS Conference – Sustainable Solutions for Our Future. October 25-28, 2015 in Atlanta, Georgia.
- International Bioenergy and Bioproducts Conference 2015 – 10/28 – 10/30 Atlanta, United States
- 3rdAnnual National Bioenergy Day
- November
- April
08 Jun 2015
Grass Energy in Vermont
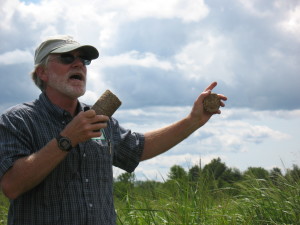
University of Vermont Extension Agronomist, Sid Bosworth explains in the field his research into use of grasses for combustion and thermal energy
In 2008, the Vermont Bioenergy Initiative began to explore the potential for grasses energy grown in Vermont to meet a portion of the state’s heating demand and reduce the consumption of non-renewable fossil fuels. The Grass Energy in Vermont and the Northeast report was initiated by the Vermont Sustainable Jobs Fund, and carried out by its program the Vermont Bioenergy Initiative, to aid in strategic planning for future grass energy program directives.
Grass Energy in Vermont and the Northeast summarizes current research on the agronomy and usage potential of grass as a biofuel, and points to next steps for the region to fully commercialize this opportunity. The keys to commercializing grass for energy are improving fuel supply with high-yielding crops, establishing best practices for production and use, developing appropriate, high-efficiency combustion technology, and building markets for grass fuel.
Perennial grasses, while serving as a biomass feedstock for heating fuel, also have numerous other benefits to farmers. The grass energy benefits reviewed in the report include retaining energy dollars in the local community, reducing greenhouse gas emissions from heating systems, improving energy security, providing a use for marginal farmland, and reducing pollution in soil and run-off from farms.
Regional and closed loop processing were two models recommended by the report, both involving farmers growing and harvesting grass, but differing in where the grass is processed into fuel and where it is used. The regional processing model calls for aggregating grass from a 50-mile radius at a central processing facility, where the grass is made into and used as fuel, or sold to local users. The closed loop model suggests farmers growing and processing grass on-site for on-farm or community use. Other models, like mobile on-farm processing and processing fuel for the consumer pellet market have significant hurdles to overcome if they are to be successful in Vermont.
In the below video a Vermont agronomist explains switchgrass production followed by entrepreneurs turning bales of grass into briquette fuel. This grass biofuel feedstock can be grown alongside food production on marginal agricultural lands and abandoned pastures, and in conserved open spaces. The harvested grass can be baled and used as-is in straw bale combustion systems, or it can be compressed into several useable forms for pellet fuel combustion systems.
For more information on grass biofuel feedstocks and to read the full Grass Energy in Vermont and the Northeast report visit the grass energy section of the Vermont Bioenergy website.
01 Jun 2015
Food Versus Fuel – Local Production for Local Use – Biodiesel as Part of Sustainable Agriculture
Nationally, corn-based ethanol and palm oil based biodiesel are gaining negative attention for their impacts on the environment and food security. But here in Vermont, farms are producing on-farm biodiesel to power equipment and operations on the farm and the local farm community. This is a profoundly different model from national and international biofuel production. Agricultural Engineering and Agronomy Researchers at University of Vermont Extension in partnership with farmers and the Vermont Bioenergy Initiative have developed a model of local minded, on-farm production of biofuels that can help rural communities transition away from unsustainable models of food, feed and fuel production.
National and global models of corn-ethanol and soy oil-biodiesel production are resulting in large-scale land conversions in some parts of the world, in particular to a loss of native grass and forestland. This type of biofuel production is not happening in Vermont, where bioenergy production incorporates rotational oilseed crops like sunflowers and soybeans on Vermont farms.
Locally produced biodiesel supports resiliency in Vermont, a cold climate state which is particularly dependent on oil. Over $1 billion leaves the state for heating and transportation fuel costs. Heating and fuel independence by producing on-farm biodiesel provides farmers fuel security which is comparable to that which is sought by Vermont’s local food movement.
The local production for local use model results in two products from one crop: oil and meal (animal feed or fertilizer). By growing oilseed and pressing the seed to extract the oil, farms are creating a valuable livestock feed at home, rather than importing it. The oil can be sold as a food product, used directly in a converted engine or converted to biodiesel for use in a standard diesel engine. In this way, oilseed crops offer flexibility in the end-use of the products. US corn-based ethanol mandates are raising grain costs nationally, making feed expensive for Vermont farmers. Local bioenergy production means farmers produce their own feed, fuel, and fertilizer for on-farm use, at a fraction of the cost and more stable prices. Reduced and stable prices for feed, fuel, and fertilizer can mean improved economic viability for Vermont farms and more stable food prices for Vermont consumers in the future.
Overall viability can be seen in the local production for local use model by considering economics, energy and carbon emissions. Biodiesel production costs of between $0.60 and $2.52 per gallon have been estimated for farm-scale production models, which are generally below market price for diesel fuel. The net energy return in Vermont on-farm biodiesel operations has been estimated at between 2.6 and 5.9 times the invested energy (i.e. more energy out than was required to produce the fuel), demonstrating strong returns and potential for improvement with increased scale. Furthermore, oilseed-based production of biodiesel has been estimated to result in a net reduction of carbon dioxide emissions of up to 1420 lbs. per acre, the equivalent of about 1500 miles of car travel per year.
Categorizing the Vermont biofuel model with national models and trends is inaccurate, considering the innovative and efficient systems benefiting Vermont farmers. While national and international analysis weighs the benefits of food versus fuel, the model is quite unique in Vermont and the food versus fuel challenge is well met. The model developed in Vermont does however have wider-reaching implications in that this can be replicated in rural farm communities across the US.
As John Williamson of Stateline Farm, a Vermont Bioenergy grant recipient says, “100 years ago everyone produced their own fuel; we are just doing that now in a different way.”
19 May 2015
Mitigating Potential Biomass Feedstock Pests
The Vermont Bioenergy Initiative aims to connect diversified agriculture and local renewable energy production for on-farm and community use by supporting research, technical assistance, and infrastructure development in emerging areas of bioenergy including biodiesel production and distribution. As we move into the growing season, there are a variety of pests that can potentially affect sunflower, canola, and soybean biomass feedstock production. In this video a University of Vermont agronomist explains how to control theses potential biomass feedstock pests and increase crop, and eventually biofuel, yields without heavy reliance on pesticides and herbicides.